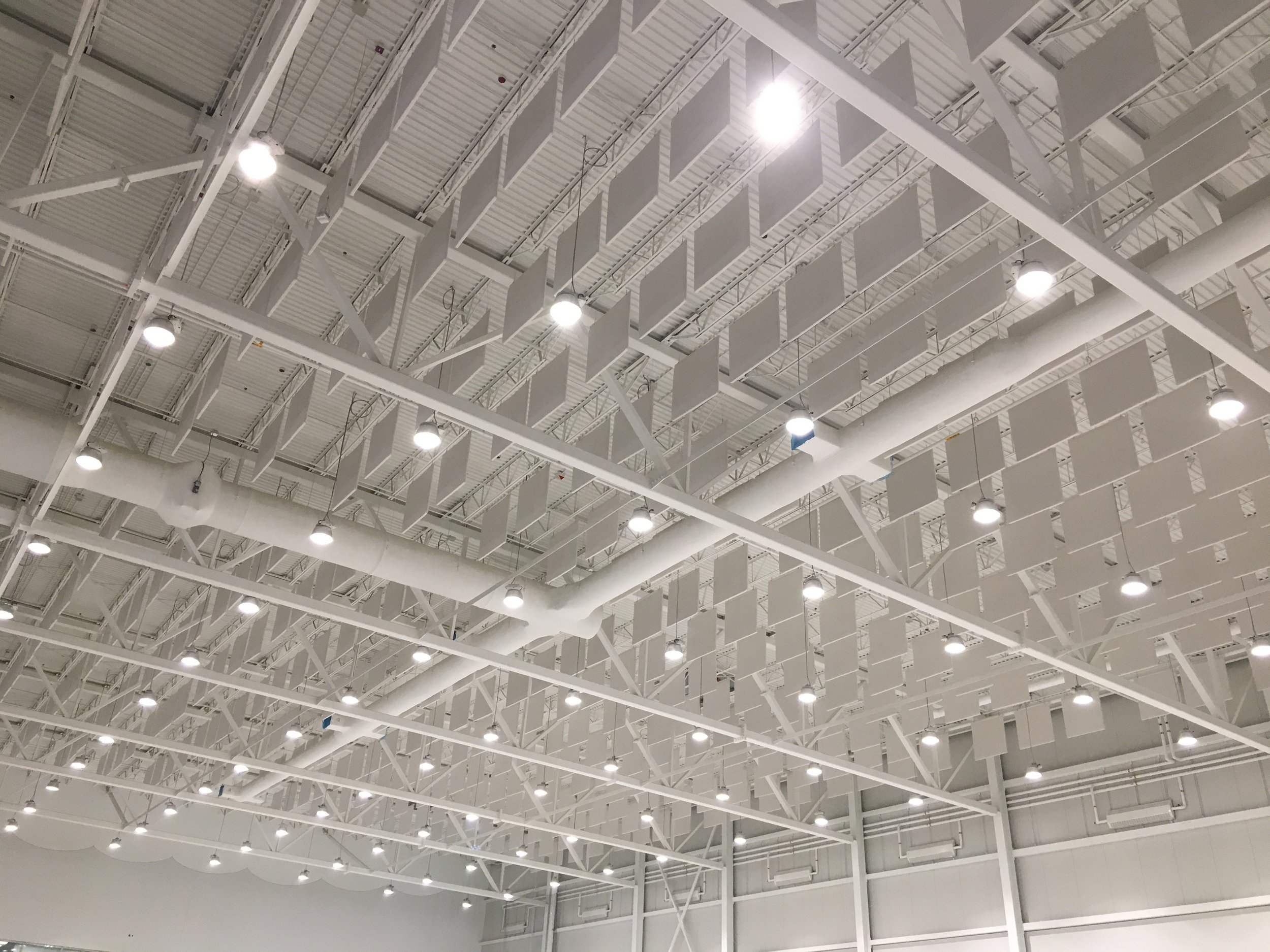
PART 1 – GENERAL
1.1 SUMMARY OF PRODUCT
A. Acoustic Baffles manufactured with formaldehyde-free medium density acoustic insulation that meets all relevant CAN/ULC, ASTM, and CGSB material standards and is GREENGUARD Children & Schools Certified.
1.2 SUBMITTALS
A. Shop Drawings: Show fabrication and installation details for acoustic baffles, including plans, elevations, sections, details and attachment to other work.
B. Submittals: Furnish samples, showing manufacture full range of colors, texture and patterns available for each type of acoustic product specified.
C. Qualification Data: For firms specified in “Quality Assurance” Article to demonstrate their capabilities and experience.
D. Product Certificates: Signed by manufacturer certifying that the products furnished comply with requirements.
1.3 QUALITY ASSURANCE
A. Manufacturer and Installer Qualifications: Manufacturer and Installer shall have a minimum of 5 years experience in producing and installing specified products and shall furnish supporting documentation showing completed jobs of approximately the same size and scope.
1.4 DELIVERY, STORAGE, AND HANDLING
A. Protect acoustic baffles from water, rain, and/or snow when shipping/handling.
B. DO NOT drag baffles across surfaces as fabric/baffle damage/soiling can occur.
C. 2 people are to carry baffles packaged in 5-packs 1200mmx1200mm in size and larger.
D. Only install acoustic baffles when building is enclosed and HVAC is operational.
E. Do not install acoustical baffles until wet work is complete and dry.
F. Install baffles after painting and flooring is completed and/or installed.
PART 2 – PRODUCTS
2.1 BAFFLES, GENERAL
A. The manufacturer’s acoustic baffles shall be made with medium density formaldehyde-free fiberglass wrapped with acoustically transparent fabric.
1. Product Model: Echotrol™ 2” Acoustic Baffle
Western Noise Control
Edmonton, Alberta, Canada
Ph. (800) 661-7241
Fax (780) 426-0325
E-mail: info@acousticsolutions.com
2. Facing Materials: Acoustically Transparent Fabrics as per Architect or heavy-duty white breathable vinyl coated textile scrim.
3. Baffle Thickness: Nominal 2” thick baffles.
4. Noise Reduction Coefficient: NRC of 0.80 for 2”.
5. Baffle Width: For cost efficiency and aesthetics, up to 1,220 mm (48 inches/4 ft) with a maximum width of 2,440 mm (96 inches/8 ft).
6. Baffle Height: For cost efficiency and aesthetics, up to 1,220 mm (48 inches/4 ft) with a maximum of 2,440 mm (96 inches/8 ft) as long as the width does not exceed 1,220 mm (48 inches/4 ft). The most economical baffles are 1,220 mm x 1,220 mm as acoustic medium density insulation is most commonly manufactured in 1,220mm x 1,220mm board sizes.
2.2 CONSTRUCTION
A. The acoustic baffle product shall be supplied in widths and lengths as indicated. All surfaces will be fully wrapped with mounting as indicated.
2.3 MOUNTING
A. Mounting Accessories: Manufacturer’s standard accessories for securely mounting baffles of type and size indicated and complying with the following requirements:
1. Ceilings: Factory-installed grommets are provided in the baffle along with a proprietary fastening assemble engineered for the specific ceiling baffles are being hung from. Ceiling substrate fasteners must be as per manufacturer’s specification to ensure loading is engineered so baffle cannot fall off ceiling. No adhesive is required for ceiling baffles.
2.4 ACOUSTIC PERFORMANCE
Sound Absorption: Per ASTM C–423 Type A Mounting
2” Thick Sound Absorption Coefficient per Octave Band Center Frequency
125Hz 250Hz 500Hz 1000Hz 2000Hz 4000Hz NRC
0.22 0.45 0.79 0.93 0.96 0.96 0.80*
*Note: Average NRC is based on the 250,500, 1000, and 2000 Hz
frequency bands and rounded to nearest multiple of 0.05. Also note
that sound absorption for a vertically hung Acoustic Baffle is significantly higher than that of a wall/ceiling mounted Acoustic Panel given its larger (approximately double) exposed surface area. Large rooms with high ceilings require both ceiling baffles and wall panels to achieve significant reductions in reverberation/echo.
2.5 SURFACE BURNING CHARACTERISTICS
A. All components pass flame spread and smoke development tests for CAN/ULC S102-M88 and/or ASTM E84 Class 1/A, NFPA 255, and/or NFPA 260 (Class 1).
PART 3 – EXECUTION
3.1 INSTALLATION
A. Install acoustic baffles in locations indicated and in alignment with other baffles. Comply with manufacturer’s written instructions for installation of baffles using type of mounting accessories indicated or, if not indicated, as recommended by manufacturer.
3.2 CLEANING
A. After completion of installation of baffles, remove dust and other foreign material with a horse hair duster brush mounted on a vacuum cleaner. A damp cloth with mild detergent and warm water or foam/pure water-free solvents can also be used for heavier soiling BUT an inconspicuous section on the side of the baffle should be tested beforehand when “wetting” the baffle/fabric with anything.